The pilot-coker consists of a feed tank and circulation system, and a furnace containing both the preheater and the coke drum. The feed drum holds at least 5 gallons and is mounted on a scale. The outlet of the drum goes to a pump and then a booster pump with the lines being steam traced. From the booster pump, the resid can flow back to the feed tank, to a slop tank or to the furnace. Initially the flow is back to the feed tank to circulate feed and stabilize the temperature. Once the unit is lined out the feed can be switched to a slop tank to check the flow rate (based upon the loss of weight measured by the scale). If the rate is correct, flow is sent to the furnace. In the furnace are first a preheater coil (mimicking the commercial furnace) followed by a coke drum. The coke drum, with dimensions of 3″ x 40″ and a volume of ~4,750 cc, is located in the furnace to prevent heat loss. Commercial coke drums are well insulated and have a high volume-to-surface area ratio, making them adiabatic. To simulate commercial steam injection water can be injected upstream of the preheater coil.
The main objectives for utilizing this reactor are to:
- reproducibly mimic commercial operation producing sufficient quantities of coke, liquids and gases for testing,
- investigate and correlate the effect of feedstock composition and reactor conditions on product rates and compositions and on coke morphology,
- maximize distillate product production and minimize coke and gas production,
- find ways to reduce tube fouling,
- develop and validate a model(s), and
- investigate scale-up issues.
This reactor is the workhorse in this Joint Industry Project (JIP) experimental investigation.
The pilot unit was modified to study foaming by adding a larger furnace, a gamma densitometer and a lift. The gamma densitometer is used to measure the density of the gas, foam, liquid layer, and coke columns in the drum. The data, as a function of height is displayed on the control monitor for each scan. Time, drum location and the corresponding density are recorded in an Excel spreadsheet. A Macro was built that plots the data as height vs. density as a function of time and density as a function of time vs. height in the drum. This set up allows the researchers to establish and track, via the forklift, the interfaces and densities as a function of time. The system is automated with a Labview control system.
To obtain a continuous flow of steam, the pulsating pump used in the parametric study was replaced with the HPLC pump that injects continuously. The antifoam is injected using an Eldex Metering Piston pump.
Operating Conditions
Temperature 850 to 950 °F
Pressure 6 to 70 PSIG
Sample Volume 10 Gallons
The DCU is operated much like an IDC. It is used as a tool to evaluate the overall coker performance of various feeds and blends at different operating conditions. Data is collected for coker product yields, furnace fouling, foaming, coke morphology and quench effectiveness.
Specifications
•2 Coke drums (3” x 72”)
•Online gas measurement/ analyzer
•A lift operated moving gamma densitometer
•Pressure capability up to 70 Psig
•Maximum Temperature 970 oF
•Flow Range 1.2 – 10 kg/hr
•Typical test duration 5 hrs
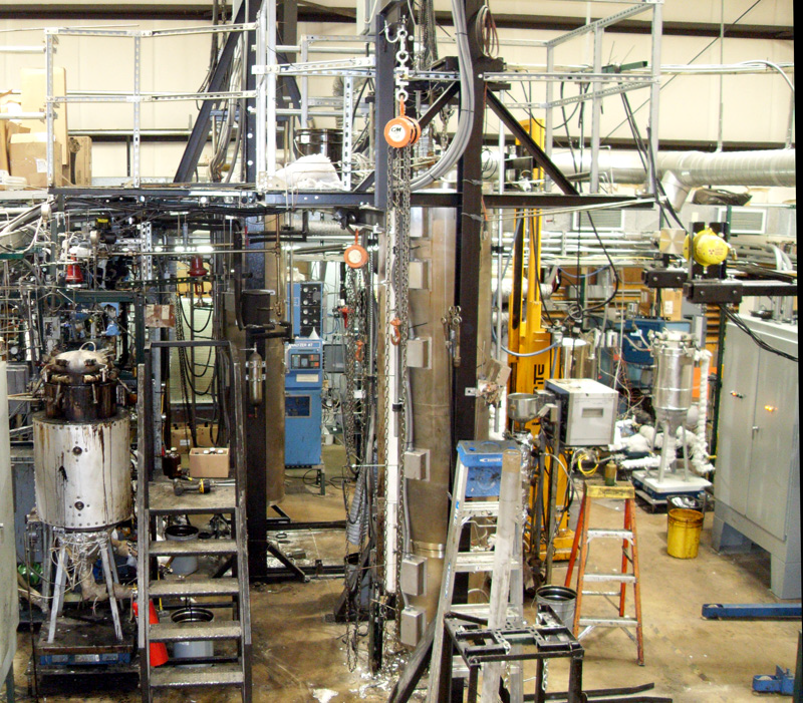
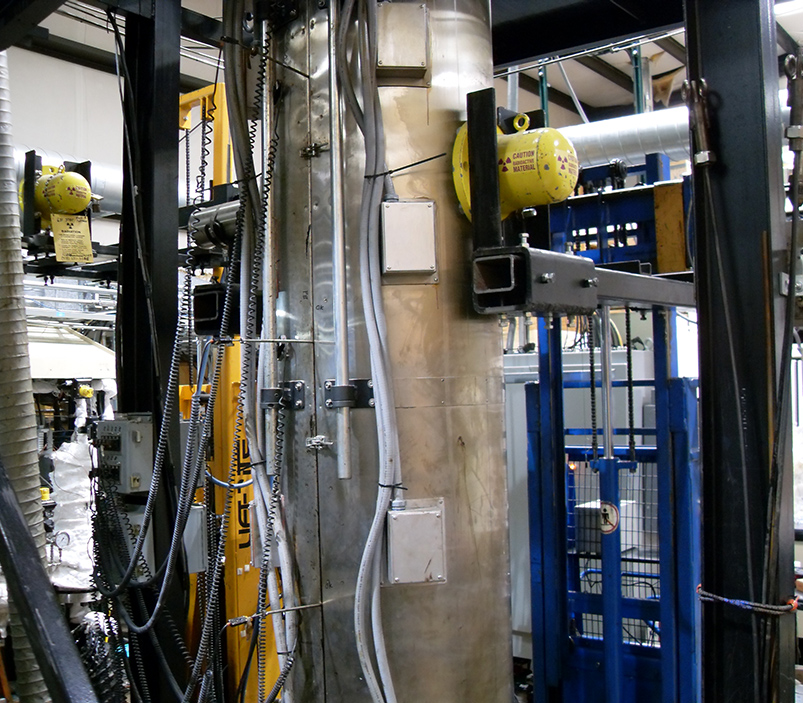