MISSION
The downstream efforts at TU started in 1999 when the coking JIP was formed. Since that time, the downstream program continued growing in an attempt to become technologically comprehensive. The second component added was the crude distillation unit which is a mix of two different technologies; the VLSD built in 2013 and the vacuum distillation unit purchased from BP in 2017. BP also provided the third component, hydrotreating capabilities, with the 2017 acquisition. The final major components are the thermal cracker built by TU and the SDA unit purchased from Foster Wheeler. These facilities provide all the pieces for TU’s state-of-the-art integrated research facility that is relevant for probing and solving problems currently facing the petroleum industry. This is a unique combination that does not exist at this scale in any other educational institution. As a result, the refining technologies group has grown into a petroleum upgrading group whose mission is to advance the upgrading of crude oils and heavy oils through in-depth targeted research using both bench level and pilot level facilities.
ABOUT THE FACILITIES
Due to tighter regulations on the international scale and the constantly changing field for the supply of petroleum products, TU’s research facility with easily reconfigurable pieces is a great advantage for industry members. As shown in the diagram below, vacuum resid may be processed several different ways after crude distillation, starting from full upgrading through deep thermal cracking in the delayed coker pilot plant or through mild thermal cracking in the visbreaker for a partially upgraded material. Alternately, a solvent extraction procedure may be followed for processing the vacuum resid through the SDA. The hydroprocessing unit adds versatility to the whole mix. It processes lighter feeds in the fixed bed mode and with some upgrades process heavier feedstocks in the slurry phase mode. Heavy product from any of the units could be processed in a variety of ways to meet research needs of (i) Improving product quality for transportability, (ii) Improving product yields and profitability, and (iii) Changing contaminant concentrations to meet regulatory standards. Due to the versatility of the integrated approach, you can start with different feedstocks from crude to bitumen to heavy residue at any stage of processing. This facility also serves as an excellent training tool for undergraduate and graduate students, external researchers, and oil companies alike. Being a pilot scale facility also allows students to have hands on experience with equipment that are a closer representation of the industrial scale equipment.
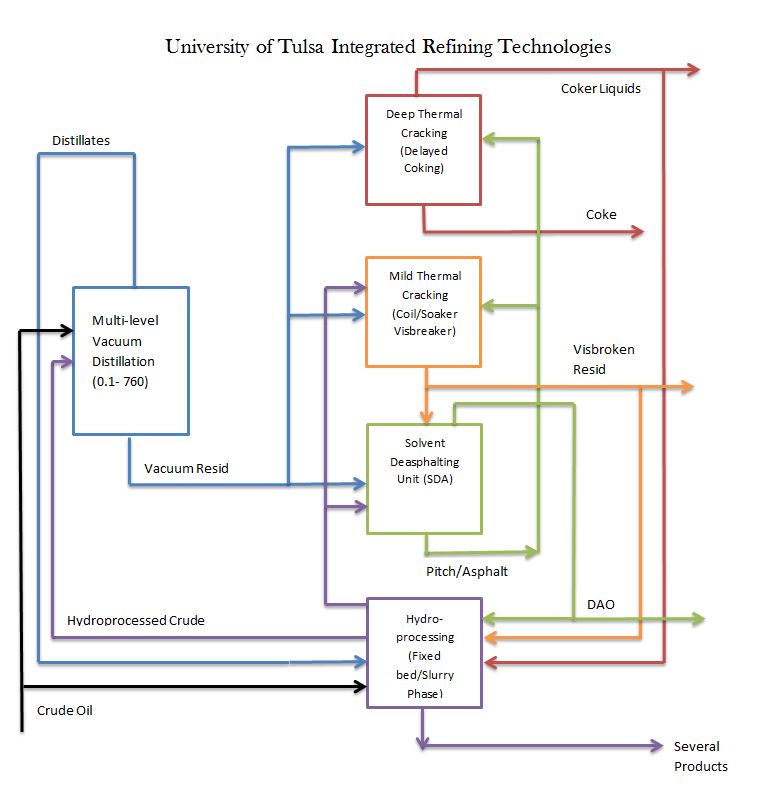